
Content Not Found
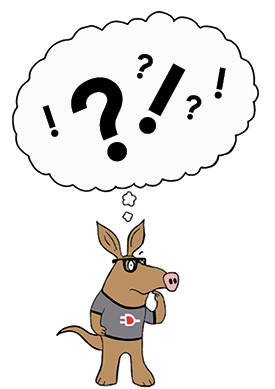
We’re sorry…
The content you are looking for cannot be found.
The link you followed may be broken, or the webpage may have been removed or had its name changed.
Please try the following:
- Make sure that the website address displayed in the address bar of your browser is spelled and formatted correctly.
- If you reached this page by clicking a link, contact the Website Administrator to alert them that the link is incorrectly formatted. Please copy-and-paste the website address displayed in the address bar of your browser into your message.
- Visit the Beckwith Electric Website Site Map.
- Visit the Beckwith Electric Website Homepage.